近日,工信部对外公布《“十四五”工业绿色发展规划》,阐述了“十四五”期间工业绿色发展的总体思路,明确了碳排放强度持续下降、污染物排放强度显著下降、能源效率稳步提升等发展目标和具体工作安排。规划明确,到2025年,工业产业结构、生产方式绿色低碳转型取得显著成效,绿色低碳技术装备广泛应用,能源资源利用效率大幅提高,绿色制造水平全面提升,为2030年工业领域碳达峰奠定坚实基础。
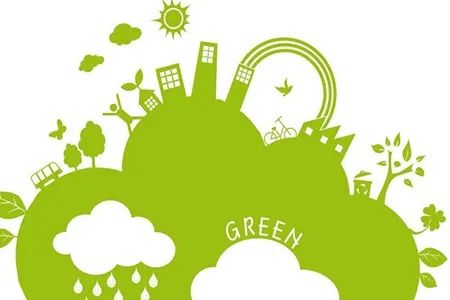
数字化转型已成为制造业生存和长远发展的“必修课”
提及制造业,它是国民经济的主体,是立国之本、兴国之器、强国之基。是国民经济的支柱产业,是国家创造力、竞争力和综合国力的重要体现、它不仅为现代工业社会提供物质基础,为信息与知识社会提供先进装备和技术平台,也是实现具有中国特色军事变革和国防安全的基础。
新中国成立尤其是改革开放以来,我国制造业持续快速发展,建成了门类齐全、独立完整的产业体系,有力推动工业化和现代化进程,显著增强综合国力,支撑世界大国地位。然而,与世界先进水平相比,中国制造业仍然大而不强,在自主创新能力、资源利用效率、产业结构水平、信息化程度、质量效益等方面差距明显,转型升级和跨越发展的任务紧迫而艰巨 。
随着新一代信息技术与制造技术的融合,给世界制造业带来了深刻变革,同时,我国的经济发展也进入了新常态,资源环境和要素成本约束也日益紧张,经济发展环境发生了重大变化。面对全球产业格局的重大调整,国际贸易规则的重构,我国制造业发展面临着严峻的外部形势。为此,国家做出一系列重大战略部署。2015年印发《中国制造2025》的通知,以“以大变强”为核心,结合我国制造业发展实际和未来制造业发展的根本要求,提出实现制造强国“三步走”战略目标,通过创新驱动、智能转型、强化基础、绿色发展几个方面加快从制造大国转向制造强国,以实现我国制造业由大变强的历史跨越。
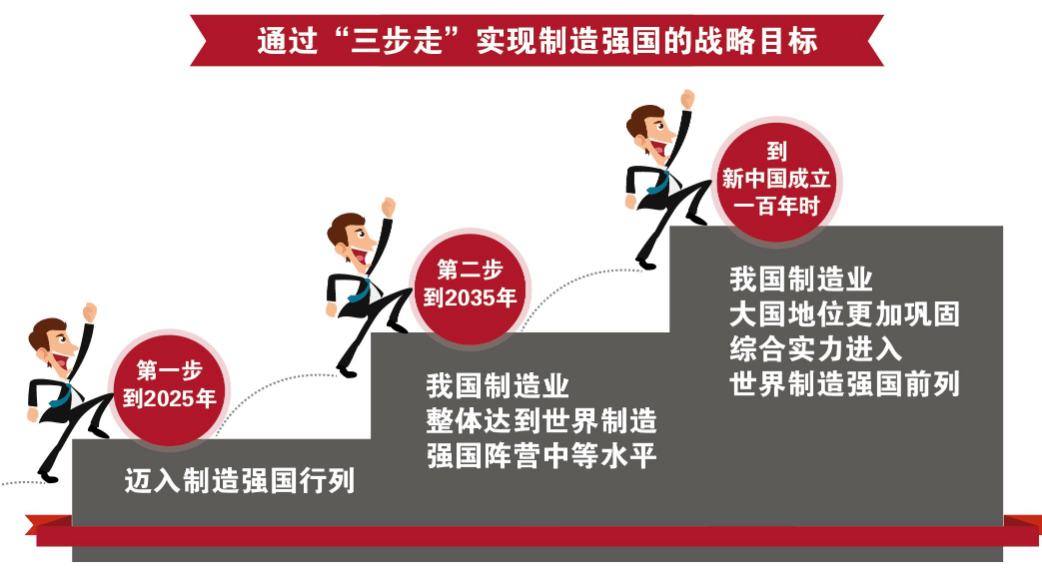
在国家政策的推动下,我国制造业也在迅速发展。2017年,我国工业增加值为279997亿元,比2016年增加6.4%,其中六大高耗能行业的增加值增长3.0%,占工业增加值的29.7%。但是,制造业发展在带动经济增长同时,也对环境造成一定的危害。制造业的大规模集聚造成对资源的过度消耗,造成严重的环境污染。对于制造企业而言,研发绿色低碳技术,实施绿色智能转型,寻找新的业务增长点对企业长久发展便显得尤为关键。
此次《“十四五”工业绿色发展规划》(以下简称“《规划》”)的发布和2035年远景目标纲要提出,制定2030年前碳排放达峰行动方案。这便意味着我国将更加坚定地贯彻新发展理念,加快制造业转型升级,走上绿色、低碳、循环的发展路径,实现高质量发展。对于制造业发展而言,数字化转型已不是“选择题”,而是关乎生存和长远发展的“必修课”了。
双碳目标下 铸造行业该如何转型?
碳中和影响着全球产业链重构,产业转型升级关系着企业的生存发展,“双碳”目标无论对国家还是制造企业而言,都是一个莫大的挑战,同样也是一个“战略”机会,对此,企业应如何抓机遇,用机遇,把绿色发展机遇转化为企业发展实力,转化为企业的竞争力?在《规划》中提出了推进产业结构高端化、能源消费低碳化、资源利用循环化、生产过程清洁化、产品供给绿色化、生产方式数字化6大转型方向,给制造企业明确了发展路径。
铸造行业是制造业的基础,各行业的发展都离不开铸件。从汽车、机床、农业机械、冶金矿山设备,到航空、航天、国防工业,乃至建筑五金、家用生活器具等行业,每年都需要大量的铸件。在我国,近20年来,国家制造业的迅速发展,对铸件的需求量增长很快,由于市场需求的拉动,铸造企业数量也迅速增加,所以对资源的耗损及环境的污染造成了很大的压力。铸造行业也由此背上了耗能大户和污染大户的标签。如何改变现状,走绿色智能转型路径,是铸造企业需要思考的课题。
要素布局、技术研发、产品设计、生产管控,贯彻绿色发展理念,落实绿色发展措施,传统铸造实现绿色智能转型的路径到底该怎么走?
首先要源头控制,不断优化能源结构和工艺流程,发展低碳能源和清洁生产,淘汰低效产能,落实好产能置换,严控新增产能。
然后通过技术赋能,加快绿色低碳技术创新和推广应用,提升节能降碳能力,加大新一代信息技术的应用,强化数字化、智能化的应用和管理,降低冗余能耗。
最后通过优化供给质量,调整业务结构和产品结构,提升产品供给质量,减少无效低效供给,减少资源浪费。
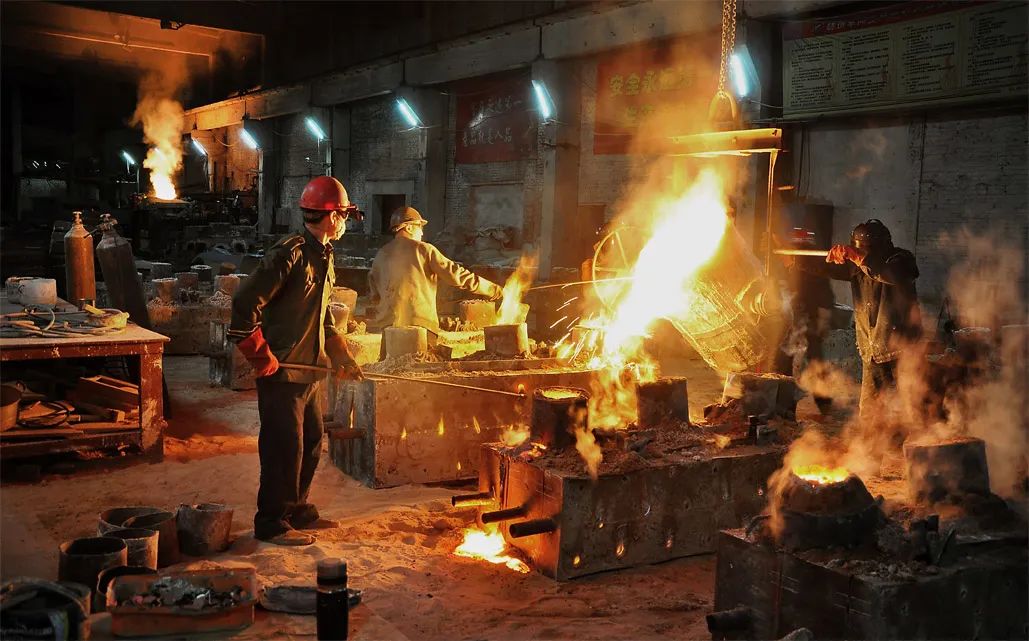
龙头企业积极探索 推广带动行业绿色智能转型
为了彻底改变铸造业的形象,中国铸造行业龙头企业共享集团开始探索研发,寻找行业转型升级的最佳路径,着力突破“卡脖子”技术,最终探索出通过3D打印产业化应用来改变传统铸造生产方式,助推传统铸造实现绿色智能转型的路径,彻底颠覆了传统铸造行业以手工为主的砂型铸造生产方式,在铸造3D打印产业化应用方面实现了国内首创,成为铸造3D打印产业化应用的“领跑者”。
3D打印产业化应用彻底改变了传统铸造“傻大黑粗”的形象,让其以“窈窕淑女”的新形象重新进入大家的视野。黑脏乱差累的“翻砂”车间消失了,以“五无”(无吊车、无模具、无重体力劳动、无粉尘及废砂排放、无温差(空调环境))铸造成形工厂与大家见面,人工重体力劳动不见了,被按钮、APP、智能机器人取代,高损耗,高成本的生产资源,被可重复利用的新材料替换,真正达到了提质降本增效、绿色智能生产的效果。
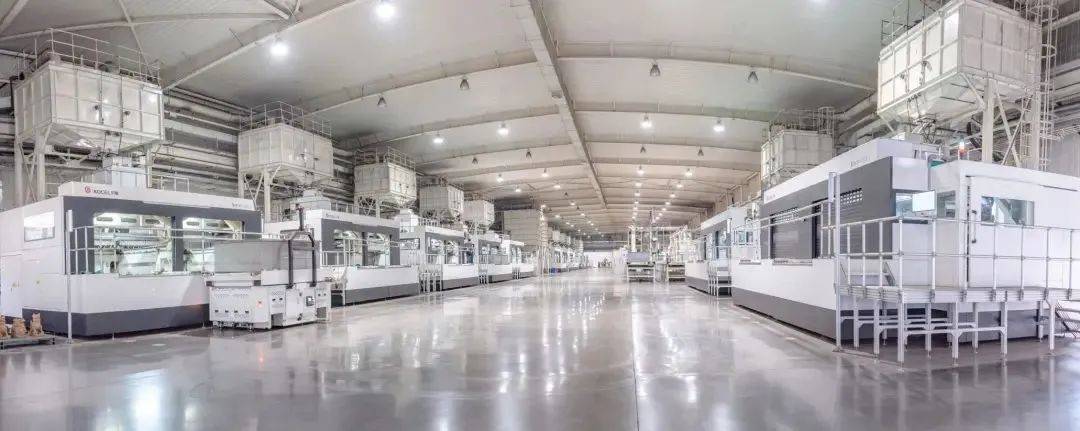
为了更好地推动铸造行业转型升级,持续为行业提供创新发展活力,2016年,在国家发改委的支持下,共享装备牵头组建国家智能铸造产业创新中心,以“引领行业进步,推动产业转型升级”为使命,开放创新资源,建立并形成关键共性技术研发、成果转移转化、产业化应用示范等运行机制,搭建开放、共享、线上线下相结合的行业平台,构筑“互联网+双创+绿色智能铸造”的产业新生态。
公司通过总结共享装备“3D打印、机器人等创新技术+智能工厂”的转型升级的经验,为铸造行业提供3D打印产业化应用解决方案。主要面向铸造行业提供铸造3D打印设备、铸造工艺设计、快速制造解决方案、铸造3D打印模具及其他3D打印产品及服务,形成“标准+示范”的带动模式。
针对传统铸造企业信息化规划薄弱、信息化孤岛严重、专业技术人员紧缺等痛点问题,国家智能铸造产业创新中心作为智能制造(铸造)系统解决方案集成商,主要为铸造行业企业提供数字化车间/智能工厂咨询规划/设计/建设/集成/总包、3D打印成套设备解决方案、智能单元建设/改造、信息化系统实施/集成等服务,助力企业数字化网络化智能化发展。
截止目前,公司已在全国建设7个基于铸造砂型3D打印的数字化工厂,在行业聚集区成立7个分中心,立足当地,充分发挥行业聚集的资源优势和辐射作用,为周边铸造产业链企业和装备制造业提供服务,不断推动产业向高端化、绿色化、智能化、融合化发展。
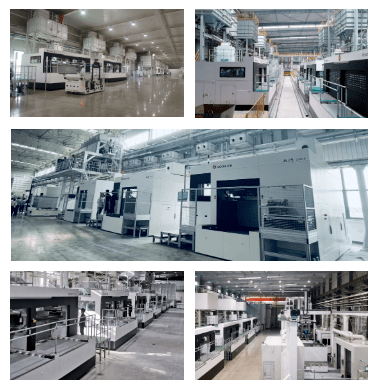
聚力企业绿色变革 助力产业低碳发展
低碳发展背景下,“双碳战略”成为企业新战略。数字技术能够助力研发设计、生产制造、运营服务等环节,从源头、过程到整体赋能节能减排,在推动企业绿色低碳转型中,起到点石成金的效果。
对于铸造企业而言,各中小型铸造企业管理、数字化、设备、人员等基础条件不同,实际生产中暴露出的痛点问题和最终呈现的结果也有所不同。如何通过数字技术助力企业在各生产环节中节能减排,向绿色低碳转型?
国家智能铸造产业创新中心通过为企业进行智能制造诊断后,根据企业实际情况采用聚焦痛点,分步推进,迭代升级的方式带动行业转型。
▷ 信息化基础较弱的中小型企业,基于总体考虑,根据企业经营痛点问题,在财务管理、生产管理、可视化管理等局部管理上实施转型带动,初步实现生产管理数字化、可视化;
▷ 有一定信息化基础的中小型企业,根据企业经营管理的需要,将产品工艺、财务管理、生产管理、质量管理等主要系统进行打通,不仅能够实现局部生产管理数字化、可视化,还能实现系统间业务集成,工艺设计基础资料、生产订单信息、检验信息等集成传递;
▷ 有一定信息化基础的中大型企业,结合企业发展需要,按照设计、制造、管理三个维度主线,帮助企业建设数字化车间/智能工厂(物联网、智能单元、智能工厂),实现工艺设计资料、生产订单信息、报工、领料、检验信息等集成传递,并且帮助企业实现对人资、体系、环境安全、设备、能源等综合管理。
双碳战略格局之下,绿色是企业数字化转型的底色,数字化转型则是绿色低碳转型的重要抓手,每个组织都承担着一份绿色使命,国家智能铸造产业创新中心愿与行业同仁携手合作,共同推进绿色低碳转型,实现绿色铸造强国梦!